催化燃燒是借助催化劑在低溫下(200~400℃)下,實現對有機物的氧化,因此,能耗少,操作簡便,安全,凈化效率高,在有機廢氣特別是回收價值不大的有機廢氣凈化方面,比如化工,噴漆、絕緣材料、漆包線、涂料生產等行業應用較廣,已有不少定型設備可供選用。
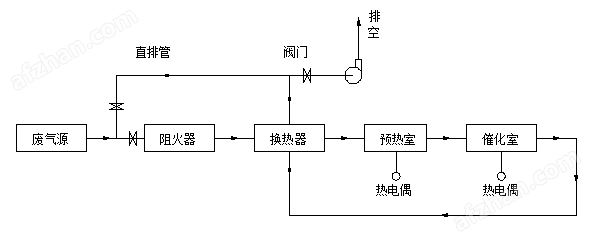
一、催化原理及裝置組成 (1)催化劑定義 催化劑是一種能提高化學反應速率,控制反應方向,在反應前后本身的化學性質不發生改變的物質。
(2)催化作用機理 催化作用的機理是一個很復雜的問題,這里僅做簡介。在一個化學反應過程中,催化劑的加入并不能改變原有的化學平衡,所改變的僅是化學反應的速度,而在反應前后,催化劑本身的性質并不發生變化。那么,催化劑是怎樣加速了反應速度呢了既然反應前后催化劑不發生變化,那么催化劑到底參加了反應沒有?實際上,催化劑本身參加了反應,正是由于它的參加,使反應改變了原有的途徑,使反應的活化能降低,從而加速了反應速度。例如反應A+B→C是通過中間活性結合物(AB)過渡而成的,即: A+B→[AB]→C 其反應速度較慢。當加入催化劑K后,反應從一條很容易進行的途徑實現: A+B+2K→[AK]+[BK]→[CK]+K→C+2K 中間不再需要[AB]向C的過渡,從而加快了反應速度,而催化劑并未改變性質。
(3)催化燃燒的工藝組成 不同的排放場合和不同的廢氣,有不同的工藝流程。但不論采取哪種工藝流程,都由如下工藝單元組成。
①廢氣預處理 為了避免催化劑床層的堵塞和催化劑中毒,廢氣在進入床層之前必須進行預處理,以除去廢氣中的粉塵、液滴及催化劑的毒物。
②預熱裝置 預熱裝置包括廢氣預熱裝置和催化劑燃燒器預熱裝置。因為催化劑都有一個催化活性溫度,對催化燃燒來說稱催化劑起燃溫度,必須使廢氣和床層的溫度達到起燃溫度才能進行催化燃燒,因此,必須設置預熱裝置。但對于排出的廢氣本身溫度就較高的場合,如漆包線、絕緣材料、烤漆等烘干排氣,溫度可達300℃以上,則不必設置預熱裝置。
預熱裝置加熱后的熱氣可采用換熱器和床層內布管的方式。預熱器的熱源可采用煙道氣或電加熱,目前采用電加熱較多。當催化反應開始后,可盡量以回收的反應熱來預熱廢氣。在反應熱較大的場合,還應設置廢熱回收裝置,以節約能源。
預熱廢氣的熱源溫度一般都超過催化劑的活性溫度。為保護催化劑,加熱裝置應與催化燃燒裝置保持一定距離,這樣還能使廢氣溫度分布均勻。
從需要預熱這一點出發,催化燃燒法于連續排氣的凈化,若間歇排氣,不僅每次預熱需要耗能,反應熱也無法回收利用,會造成很大的能源浪費,在設計和選擇時應注意這一點。
③催化燃燒裝置 一般采用固定床催化反應器。反應器的設計按規范進行,應便于操作,維修方便,便于裝卸催化劑。
在進行催化燃燒的工藝設計時,應根據具體情況,對于處理氣量較大的場合,設計成分建式流程,即預熱器、反應器獨立裝設,其間用管道連接。對于處理氣量小的場合,可采用催化焚燒爐,把預熱與反應組合在一起,但要注意預熱段與反應段間的距離。
在有機物廢氣的催化燃燒中,所要處理的有機物廢氣在高溫下與空氣混合易引起爆炸,安全問題十分重要。因而,一方面必須控制有機物與空氣的混合比,使之在爆炸下限;另一方面,催化燃燒系統應設監測報警裝置和有防爆措施。
二、催化燃燒用催化劑
由于有機物催化燃燒的催化劑分為貴金屬(以鉑、鈀為主)和金屬催化劑。貴金屬為活性組分的催化劑分為全金屬催化劑和以氧化鋁為載體的催化劑。全金屬催化劑是以鎳或鎳鉻合金為載體,將載體做成帶、片、丸、絲等形狀,采用化學鍍或電鍍的方法,將鉑、鈀等貴金屬沉積其上,然后做成便于裝卸的催化劑構件。由氧化鋁作載體的貴金屬催化劑,一般是以陶瓷結構作為支架,在陶瓷結構上涂覆一層僅有0.13mm的α-氧化鋁薄層,而活性組分鉑、鈀就以微晶狀態沉積或分散在多孔的氧化鋁薄層中。
但由于貴金屬催化劑價格昂貴,資源少,多年來人們特別注重新型的、價格較為便宜的催化劑的開發研究,我國是世界上稀土資源最多的國家,我國的科技工作者研究開發了不少稀土催化劑,有些性能也較好。 三、催化劑中毒與老化 在催化劑使用過程中,由于體系中存在少量的雜質,可使催化劑的活性和選擇性減小或者消失,這種現象叫催化劑中毒。這些能使催化劑中毒的物質稱之為催化劑毒物,這些毒物在反應過程中或強吸附在活性中心上,或與活性中心起化學作用而變為別的物質,使活性中心失活.
毒物通常是反應原料中帶來的雜質,或者是催化劑本身的某些雜質,另外,反應產物或副產物本身也可能對催化劑毒化,一般所指的是硫化物如H2S、硫氧化碳、RSH等及含氧化合物如H2O、CO2、O2以及含磷、砷、鹵素化合物、重金屬化合物等。
毒物不單單是對催化劑來說的,而且還針對這個催化劑所催化的反應,也就是說,對某一催化劑,只有聯系到它所催化的反應時,才能清楚什么物質是毒物。即使同一種催化劑,一種物質可能毒化某一反應而不影響另一反應。
按毒物與催化劑表面作用的程度可分為暫時性中毒和性中毒。暫時性中毒亦稱可逆中毒,催化劑表面所吸附的毒物可用解吸的辦法驅逐,使催化劑恢復活性,然而這種可再生性一般也不能使催化劑恢復到中毒前的水平。性中毒稱不可逆中毒,這時,毒物與催化劑活性中心生成了結合力很強的物質,不能用一般方法將它去除或根本無法去除。
催化劑的老化主要是由于熱穩定性與機械穩定性決定的,例如低熔點活性組分的流失或升華,會大大降低催化劑的活性。催化劑的工作溫度對催化劑的老化影響很大,溫度選擇和控制不好,會使催化劑半熔或燒結,從而導致催化劑表面積的下降而降低活性。另外,內部雜質向表面的遷移,冷熱應力交替所造成的機械性粉末被氣流帶走。所有這些,都會加速催化劑的老化,而其中最主要的是溫度的影響,工作溫度越高,老化速度越快。因此,在催化劑的活性溫度范圍內選擇合適的反應溫度將有助于延長催化劑的壽命。但是,過低的反應溫度也是不可取的,會降低反應速率。
為了提高催化劑的熱穩定性,常常選擇合適的耐高溫的載體來提高活性組分的分散度,可防止其顆粒變大而燒結,例如以純銅作催化劑時,在200℃即失去活性,但如果采用共沉積法將Cu載于Cr2O3載體上,就能在較高的溫度下保持其活性。 四、催化劑及催化燃燒技術 沒有催化,就不會有現代技術的世界。 因此,催化在人們的技術進步中是的。催化作用具有加速作用和定向作用。在反應之后,其催化劑本身沒有變化。
催化劑分為工業用催化劑和環保用催化劑。本公司生產的HP-C型系列環保用催化劑,主要把有機廢氣轉成二氧化碳和水。或者無害的其他氣體。
1.1.催化反應過程
1.1.1.反應物(有機廢氣)向催化劑表面擴散。
擴散是一個物理過程,它具有使濃度均勻化的傾向。由于在催化劑表面上的反應物分子消失很快,因而反應物在這里的濃度,這樣就形成一個向催化劑表面的擴散流。
1.1.2.反應物(有機廢氣)在催化劑表面上吸附。
反應物在催化劑表面的吸附有物理吸附和化學吸附。物理吸附是非選擇性的,各種各樣的分子在固體表面上進行的物理吸附能力與沸點有關。通過加熱或低壓力,被吸附的分子就立即被脫附,可逆性好,吸附熱小。化學吸附使被吸附分子與固體表面之間,形成一種與分子中間連接各個原子同樣的共價鍵或電價鍵。俗稱化學鍵已打開。大多數吸附現象,至少在低溫度下進行時是可逆的。在高溫度下發生的吸附,不能復原為起始的化合物,是不可逆的。但是,隨著催化劑技術的進步,在相對低溫下也會出現不可逆吸附。化學吸附是有高度的選擇性,吸附的化學計量關系取決于金屬吸附劑的性質,被吸附分子的性質。吸附是一個放熱過程。
1.1.3.被吸附的反應物(有機廢氣與氧氣)在表面上的相互作用。催化劑在被吸附的 反應物中起著中間橋梁作用,通過自身原子電磁場的作用,金屬自由價打開又閉合,使反應物中的化學鍵重新組合排列,形成新的化合物。
1.1.4.生成物由催化劑表面脫附。
在環保催化作用的生成必須是最終生成物即二氧化碳和水。如果氧化過程不。就會生成碳氫化合物的衍生物。有機化合物在氧化過程中是由幾個步驟組成的連續反應。當氧氣不足時,就會生成是中間生成物。因此,在環保行業中,有機廢氣的氧化反應選用蜂窩狀催化劑為好。如選用顆粒狀催化劑,顆粒間的間隙較小,顆粒狀催化劑表面氧氣不足,氧化反應不能進行,因而,生成碳氫化合物的衍生物。所以,有機廢氣的氧化必須最終產物后才能脫附
1.1.5.生成物離開催化劑表面向催化劑周圍的介質擴散。
1.2.催化劑組成
本公司生產的GSET-C型催化劑以r-A12O3蜂窩狀為載體,表面涂覆貴金屬。催化劑的備制工藝和方法,直接影響著催化劑的質量。以前,已備制出第三代催化劑,第四代催化正在研制之中。催化劑的材料是多樣化的。一般有稀土金屬和貴金屬。從形狀來看有蜂窩狀的、顆粒狀、片狀。蜂窩狀的復雜,制造成本較高。但比表面、活性,催化。催化劑另一個要求載體表面貴金屬、稀土金屬、氧化金屬的晶體顆粒越小越好。又必須與載體的分子晶體結合能緊密。其實,催化劑表面起作用的厚度為20nm~30nm。
1.3.準納米催化劑和納米催化劑
在催化劑的催化作用機理上分析。貴金屬、稀土金屬作催化劑,其涂在載體表面的催化劑的晶體顆粒直徑越小,達到納米級,就會出現納米效果。納米效應的定義為某種催化劑表面金屬顆粒直徑達到納米級并具有小尺寸效應和量子效應的。可稱為納米催化劑。第二代催化劑金屬顆粒的直徑為5nm~20nm。啟燃溫度為250~320℃,空速為20000h-1;第三代催化劑又稱準納米催化劑,貴金屬顆粒直徑為2nm~10nm,啟燃溫度為120~250℃,空速為40000h-1;第四代催化劑又稱納米催化劑,貴金屬顆粒直徑為0.7nm~2nm,啟燃溫度為60~120℃,空速為>100000h-1。
催化燃燒技術就是有機廢氣預熱到啟燃溫度在催化劑的作用下生成無毒的二氧化碳和水,并且釋放大量的熱量,整套凈化裝置的核心是催化劑。
催化劑通常是以鉑,鈀為活性金屬的貴金屬催化。同樣也可使用鈦、鈰等稀土金屬催化,在使用催化劑是根據使用溫度,催化劑的耐毒性及熱穩定性等綜合因素考慮。在各種形狀中蜂窩狀,空速為,阻力為最小,有利于催化燃燒,在處理同等風量中,催化燃燒裝置輕巧。占地面積及所占空間最小
催化活性下降的主要原因
催化劑熱老化現象:催化燃燒溫度通常是在300℃~400℃運行,當有廢氣在選型中濃度過高,或有機廢氣揮發的沖擊波峰過長,使催化燃燒爐始終保持在600℃以上運行,催化劑表面的貴金屬顆粒的移動就比較頻繁,從而產生凝聚現象。貴金屬表面的自由能下降,所以催化活性就會下降,再者,r-A12O3蜂窩載體的比表面積也會下降。
催化劑的中毒現象:遇到鹵素元素,容易使貴金屬變成氧化物而失去活性。遇到Si、P、AS、Sn等覆蓋貴金屬活性表面,從而使催化活性下降。
催化劑的污染現象:主要在有機廢氣中存在焦油、氧化物覆蓋貴金屬使活性下降。
以上幾種現象都會影響催化燃燒正常運行。
催化活性下降處理對策在催化燃燒的選型要正確判斷有機廢氣的成份及濃度,從而正確選用催化劑。經驗告訴自己判斷并作出綜合處理方法。有機廢氣治理工作經驗占有七成。催化劑活性下降,首先判斷下降的原因,然后作出正確的相應措施。
1、熱老化現象的處理:更換新品催化劑。
2、中毒現象的處理:化學清洗。
3、焦油,油霧的污染處理:熱處理。
4、對性中毒處理:要更換新的催化劑。
5、對催化劑活性有影響化合物,在凈化系統設計應加前處理系統,或者正確選用 催化劑。
正確使用催化劑壽命在2年以上,可達3~5年
1.4.催化劑的選擇
目前,使用具有代表性的催化劑有鉑、鈀鈀系列。兩者的催化溫度是不同的,鉑比鈀的催化溫度低,活性高于鈀。鉑的有機溶劑的催化溫度為200℃,象甲醇、甲醛等就可氧化。一般催化溫度在300℃才能氧化的有機溶劑有甲酚、醋酸等。所以催化溫度的選擇,首先取決于有機溶劑的成份,這樣才能正確保證凈化率和活性的持久性。在催化劑中鉑比鈀貴,因此,實際選用鈀作催化劑比較多。適當提高催化溫度。實際證明,催化溫度保證在300℃以上時,大部分有機溶劑就可以氧化。個別有機溶劑必須在350℃以上才能氧化。因此,在選擇催化溫度前,必須了解有機廢氣中有機成份,不能一概而論。如果隨意選擇溫度,那很容易造成不氧化,使有機溶劑的微粒子吸附催化劑載體的表面,久而久之,催化劑的活性就下降。直接影響凈化率的轉化。這種現象就是大家所經常碰到的催化燃燒開始時凈化率高,而過了一段時間后效果不明顯。其實,真正能掌握催化燃燒技術的工作者和企業,可以避免這種現象。
催化劑另一個重要指標就是空速。空速就是在單位時間內所處理的處理量。從形狀上看,蜂窩狀比丸狀的空速來得大。空速選擇不正確馬上影響凈化率。因此,選擇蜂窩狀才比較理想。
催化劑除了貴金屬外, 還有稀土金屬催化劑。稀土金屬系列目前我國還不夠成熟。選用單位比較少。但是它的價格遠低于貴金屬,前景廣闊。我國又是稀土金屬礦源十分豐富的國家。稀土金屬的催化作用能有效提高,這標志著催化燃燒技術性的飛躍。
催化劑的載體目前多數采用氧化鋁陶瓷。一般可分為丸狀、帶狀和蜂窩狀。在實踐應用中應該選用蜂窩狀,這是因為蜂窩狀的比表面積大、空速大、用量少(僅為丸狀的1/2),壓力損失少,而反應器的斷面積僅是丸狀的1/4。
催化劑性能比較如下表: 催化劑 項目 | 貴金屬 |
蜂 窩 狀 | 丸狀 |
空速h-1 | 40000 | 10000 |
線速度m/s | 2~2.5 | 0.4~0.8 |
壓力損失Pa | 300~400 | 600~1200 |
催化劑粉化 | 沒 | 易粉化 |
催化劑堵塞 | 沒 | 易產生 |