1. 引言
多回路電表不僅支持對單路或多路電路的實時監測,還能通過數據分析優化能源分配、預防故障發生。本文將從技術原理、核心功能、選型要點,系統闡述其在工業配電系統中的價值。
2. 多回路電表的核心功能
2.1 多回路測量與監控
多通道設計:支持4~16路獨立電路測量(如電機、泵類、照明等設備),每路數據實時隔離,避免相互干擾。
參數全面:
電壓(U)、電流(I)、功率(P)、功率因數(PF)、頻率(f)。
有功電能(kWh)、無功電能(kvarh)、視在功率(S)。
2.2 高精度數據采集
工業級精度:
電壓/電流測量誤差≤±0.2%,功率誤差≤0.5%,滿足ISO 50001能源管理體系要求。
高頻采樣:
采樣率高達1kHz,捕捉瞬時異常(如浪涌、諧波)。
2.3 遠程通信與智能化分析
通信協議:支持Modbus RTU/TCP、LoRaWAN/NB-IoT、Wi-Fi 6,無縫對接工業物聯網(IIoT)平臺。
邊緣計算:
本地運行輕量級AI算法(如異常檢測、負荷預測),減少云端依賴。
云端協同:
數據上傳至能源管理平臺(如西門子EnergyIP),生成可視化報表與節能建議。
2.4 能源管理與優化
分戶計量:對不同車間或生產線進行獨立計費,支持階梯電價策略。
能效評估:
計算設備能效比(如電機效率曲線),識別低效設備并優化啟停時間。
碳排放核算:
結合電網碳排放因子,量化企業用電活動的碳足跡。
3. 工業配電系統中多回路電表的關鍵作用
3.1 故障診斷與預防
實時報警:
檢測電壓驟降、電流越界、諧波超標等異常,觸發聲光報警并上傳至管理平臺。
故障溯源:
通過歷史數據回放,定位故障發生的時間點與電路位置(如某車間壓縮機頻繁跳閘)。
3.2 能源效率提升
負荷平衡:
分析各回路負載分布,優化變壓器容量利用率(如避免輕載運行)。
峰谷電價利用:
結合電價政策,自動調整高耗能設備運行時段(如將電爐生產移至夜間低谷期)。
3.3 成本核算與碳中和目標
精細化計費:
對生產設備、辦公區域、公共設施進行分項計費,避免能源浪費。
碳資產管理:
通過多回路電表數據,參與碳交易市場,出售綠電消納憑證。
3.4 設備生命周期管理
預測性維護:
基于電流波形分析設備磨損趨勢(如軸承振動異常預示電機即將故障)。
設備能效評級:
對老舊設備進行能效排序,優先替換高耗能設備(如S7系列變壓器升級為S11系列)。
4. 多回路電表選型指南
4.1 核心參數分析
參數類別 關鍵要求 典型值
參數類別 | 關鍵要求 | 典型值 |
測量精度 | 電壓/電流誤差≤±0.2%,功率誤差≤0.5% | ISO 50001認證 |
回路數量 | 支持4~16路獨立測量 | 根據配電復雜度選擇 |
通信協議 | 必須支持Modbus RTU/TCP + LoRaWAN | 工業物聯網用 |
防護等級 | IP67(戶外安裝)或IP30(室內) | 根據安裝環境選擇 |
工作溫度 | -40℃~+85℃ | 惡劣工業環境適用 |
4.2 功能需求匹配
(1) 基礎型多回路電表
適用場景:小型工廠、倉庫等簡單配電系統。
功能需求:
多回路測量與本地顯示。
RS485通信支持能源數據上傳。
(2) 升級多回路電表
適用場景:大型制造企業、化工園區等復雜系統。
功能需求:
Wi-Fi 6遠程控制與云端分析。
諧波檢測、負荷預測等高級功能。
預付費管理與分戶計費模塊。
5. 典型應用場景與案例分析
5.1 汽車制造工廠
需求:監測沖壓車間、焊接車間、涂裝車間等高耗能設備的用電情況。
方案:部署16路多回路電表,每路對應一臺大型電機。
效果:
發現某焊接設備空載運行時功率異常,年節省電費約50萬元。
通過負荷預測算法,將峰值用電負荷降低15%。
5.2 化工園區配電系統
需求:確保危化品生產區域的電力安全,防止因諧波引發設備故障。
方案:選用具備諧波分析功能的電表(THD≤5%),并安裝濾波器。
效果:
諧波含量從8%降至2%,設備故障率下降30%。
符合GB/T 14549-2019《電能質量 公用電網諧波》標準。
5.3 數據中心能源管理
需求:監控服務器、冷卻系統、UPS等設備的能耗,優化PUE(電能使用效率)。
方案:部署8路多回路電表,集成到DCIM(數據中心基礎設施管理)平臺。
效果:
PUE值從2.1降至1.8,年節能約200萬kWh。
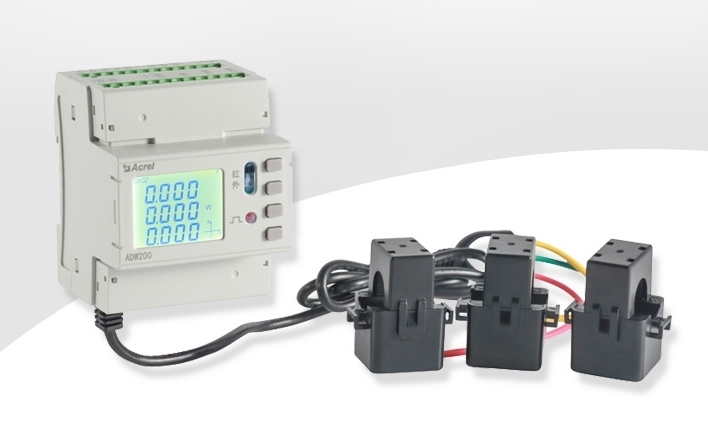